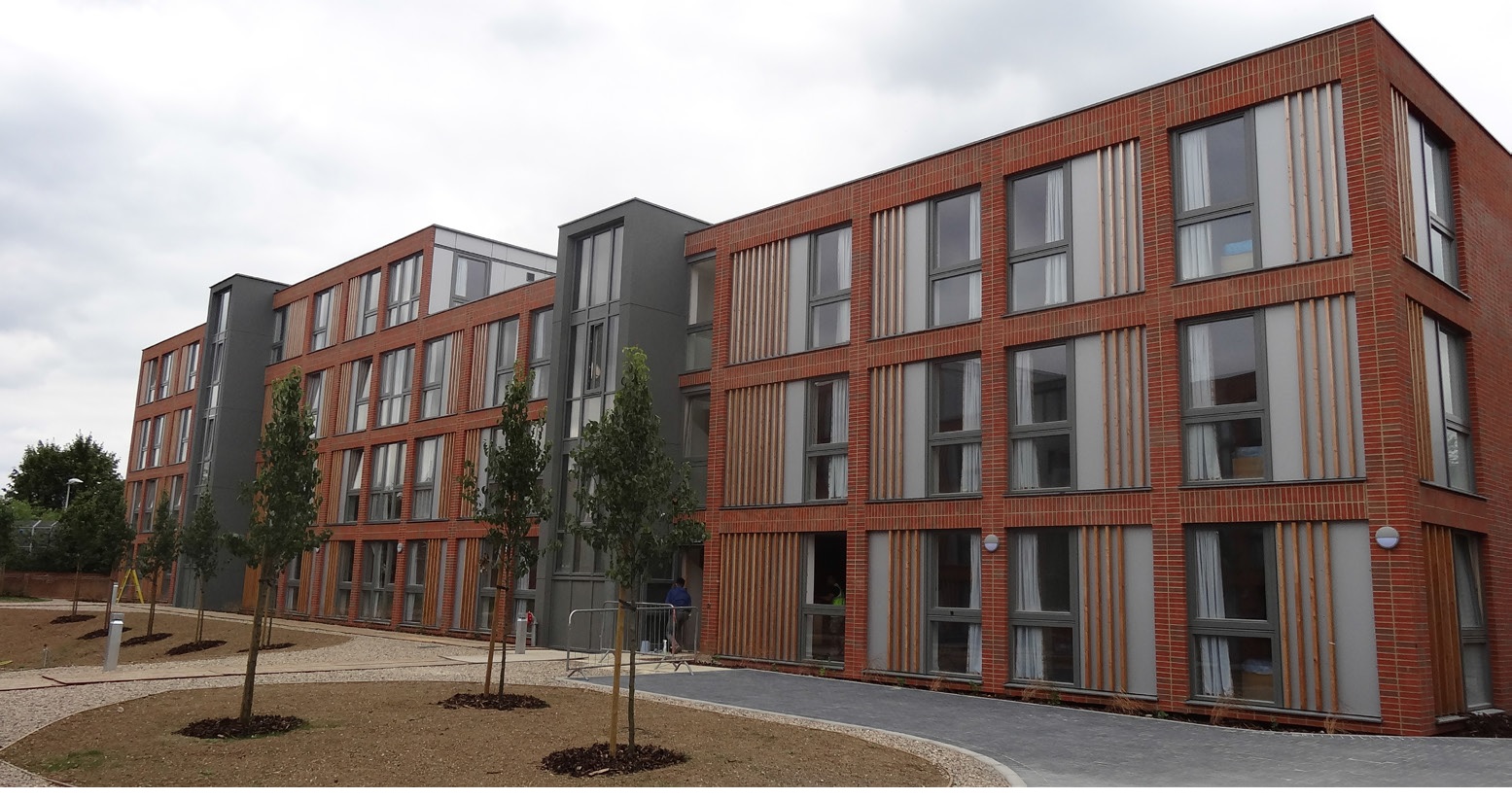
Student Accommodation – Oxford
Sustainable, high quality buildings
Project: Chapel Street
Company: EBS Elk
Sector: Education
Technology: Timber Frame
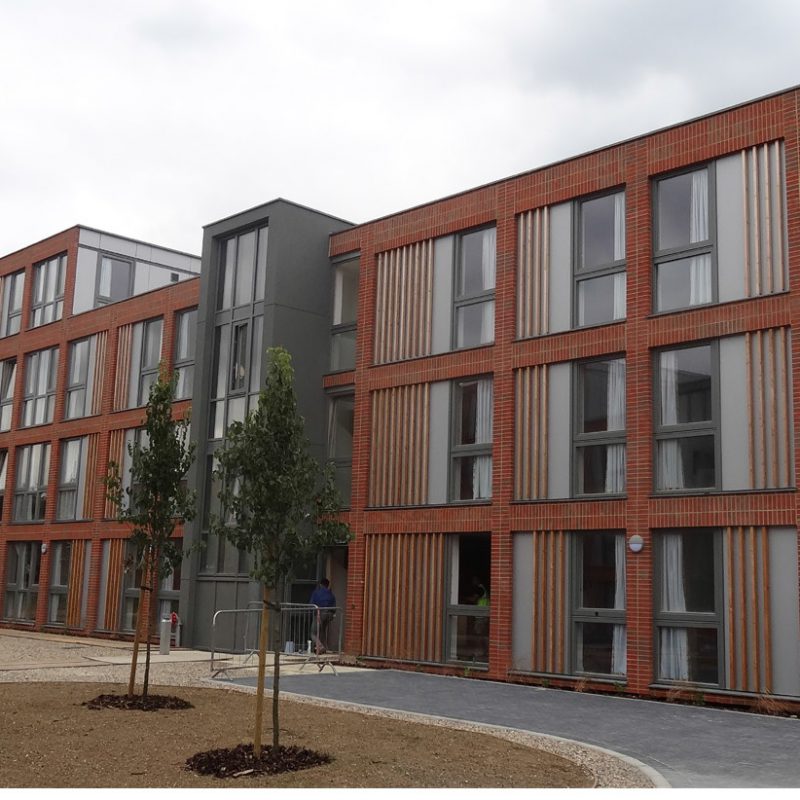
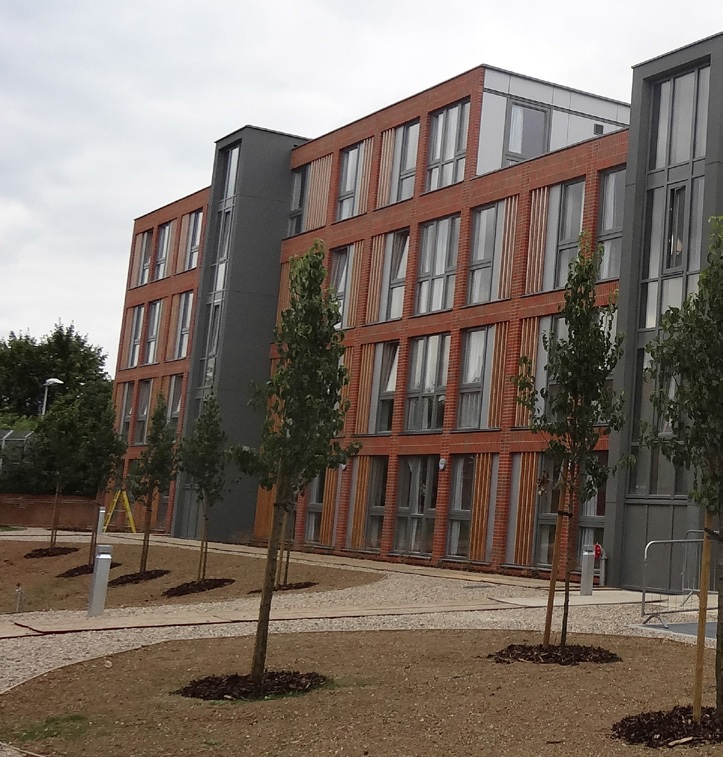
Overview:
EBS elk is one of the leading suppliers of offsite manufactured buildings in the UK. Our mission is to deliver sustainable, high quality buildings that are designed to meet the requirements of clients as well as providing solutions to the ever higher performance demands of governments and end users. The ELK system is based on structural timber panels that have their external finishes, internal plasterboards and electrical cut-outs and conduits prepared and applied in the factory. Windows are also pre-fitted.
EBS elk install these very sustainable offsite manufactured buildings which have a very low impact on the environment – all of ELK’s wall/floor/ceiling/roof elements achieve an A* rating on the BRE Green Guide to Housing. Coupled with our very thermally efficient walls/window/doors, exceptional thermal bridging rating and low air tightness, ELK produce buildings which have very low carbon emissions. This in turn reduces the energy needed to provide the hot water, heating, cooling and ventilation in the building and thereby reducing the costs to the occupier.
Project Type/Application:
With Chapel Street, a £2,5m project, EBS elk made a number of key design changes maximizing the efficiencies of offsite construction which enabled us to create a “Designed for Manufacture” building. We focused on the following qualities to save time and resources during and long after the assembly of the building:
- External walls: carrier board fixed in the factory for stack bond brick slip to be fixed to
- Internal walls: resilient bars, insulation, OSB boards and plasterboard all fitted in the factory
- Roof cassettes: EPDM membrane fixed in the factory so building is instantly water proof
- M&E design: reduced energy demand of the building meant that a redundant lift shaft could be used to house the boilers on one floor with the hot water tanks on another
- Service runs: designed to co-ordinate with bathroom pods
- Large exterior plant room: completely removed, avoiding long term maintenance issues
- 19% of 20% renewable energy demand for the building was provided by use of CHP boilers with MVHR systems due to thermal performance and airtightness of building
Outcome/Results/Success Factor:
The collaborative design process with all members of the team involved produced a building that was delivered and finished within Budget, ahead of time and exceeded expectations.