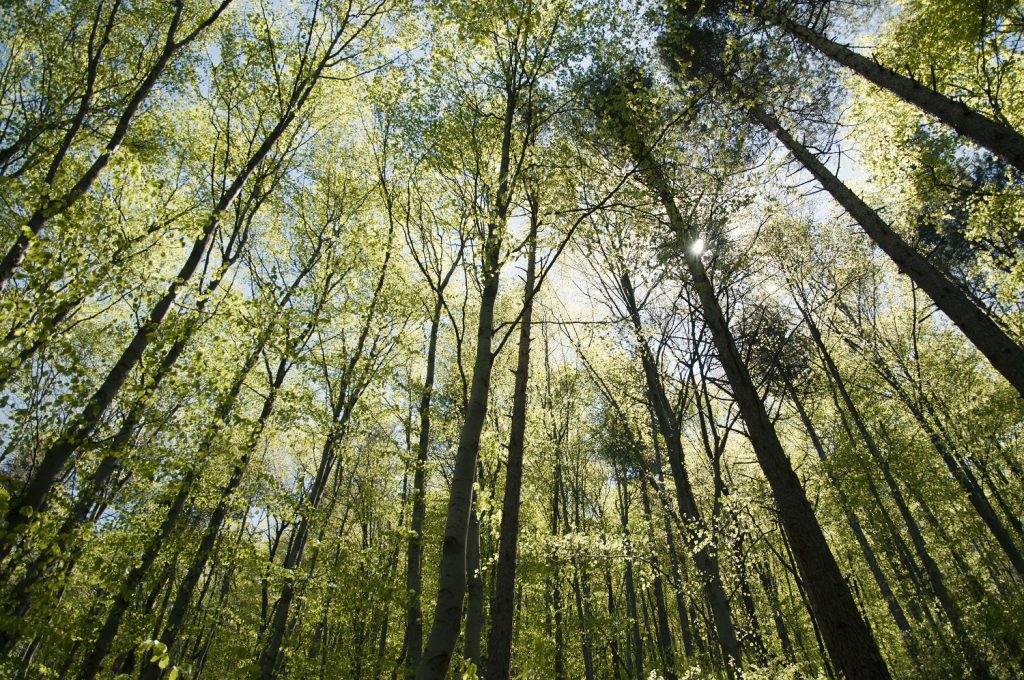
SUSTAINABILITY
Timber possesses the lowest embodied carbon of any building material
The UK’s built environment is estimated to be responsible for nearly half of the UK’s carbon emissions, and embodied carbon can account for as much as 30% of this (a figure that will only increase as buildings become ever more energy efficient).
Classified as Mass Timber, CLT (cross-laminated timber) and Glulam (glued-laminated timber), Mass timber presents an excellent opportunity to develop projects that deliver significant sustainability benefits and are known to enhance both the living and working environment, as the volume of timber used in the manufacture of these systems is high.
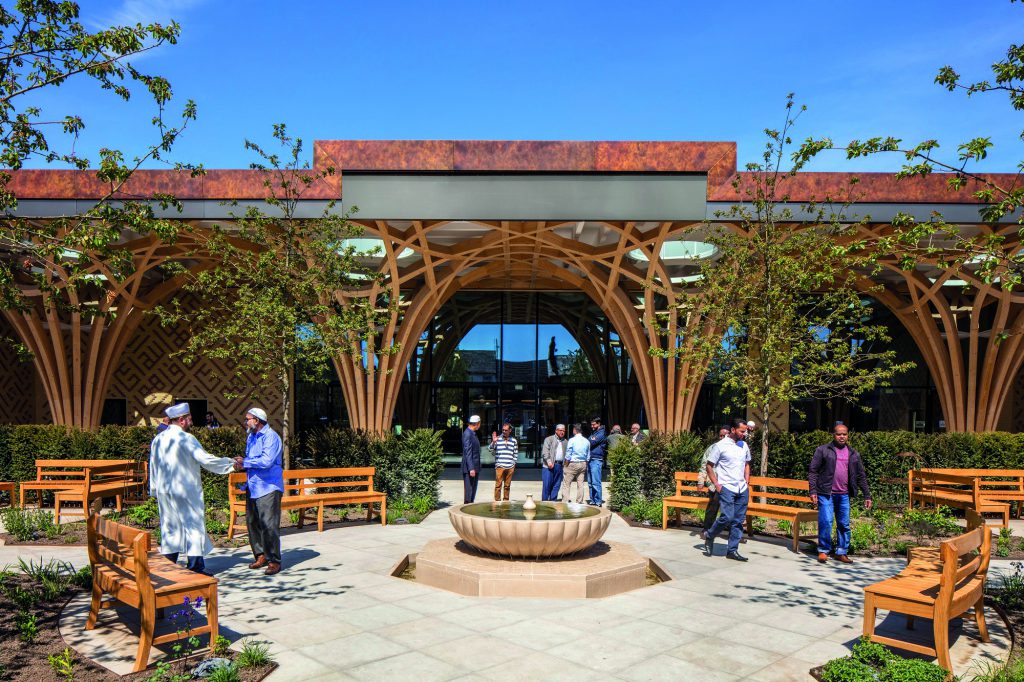
Fight Against Climate Change
The UK has positioned itself as a world leader in the fight against climate change, becoming the first major economy to legislate a Net Zero target by 2050, with an interim target of a 78% reduction by 2035. Achieving these ambitious goals will require decarbonisation across every aspect of the UK industry. The Government’s Industrial Decarbonisation Strategy, published in March 2021, made it clear that work must start today to create the foundations on which a green industrial revolution can be built.
The STA has written a White Paper that highlights the key role that timber will play in enabling the construction industry to meet the challenges of industrial decarbonisation and deliver Net Zero by 2050.
Timber and Offsite Construction
There is a drive to increase the use of offsite construction, some forms of which can encourage the use of sustainable materials such as timber. As well as delivering a significant reduction in carbon emissions, the use of timber in construction delivers other benefits, particularly concerning offsite timber frame construction. Where pre-manufactured value is under consideration, a timber frame building can represent over 30% of the building fabricated offsite.
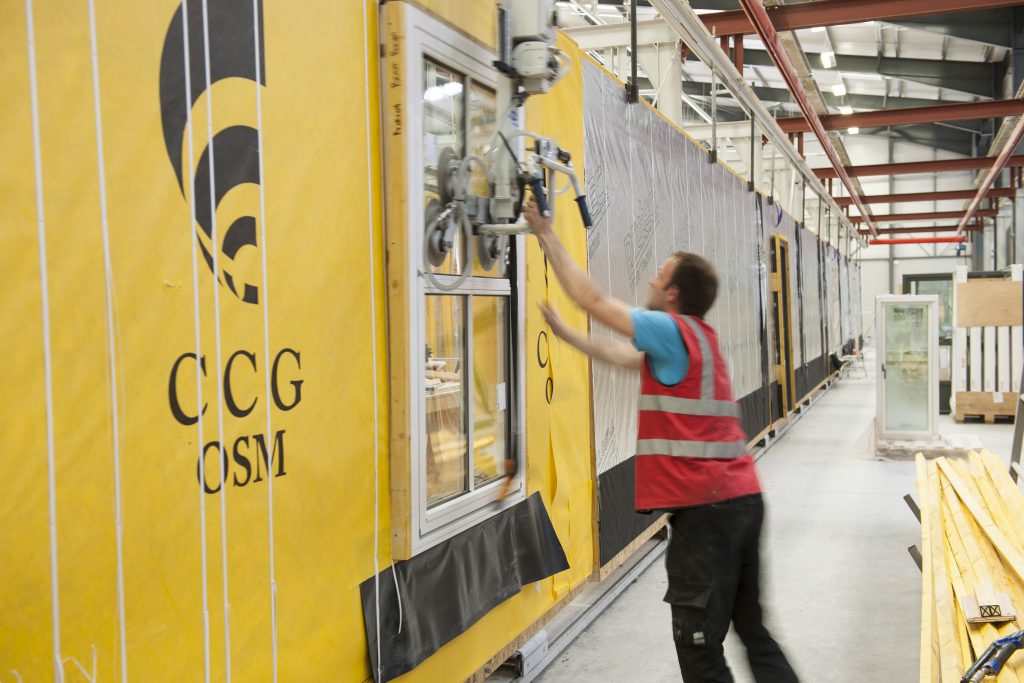
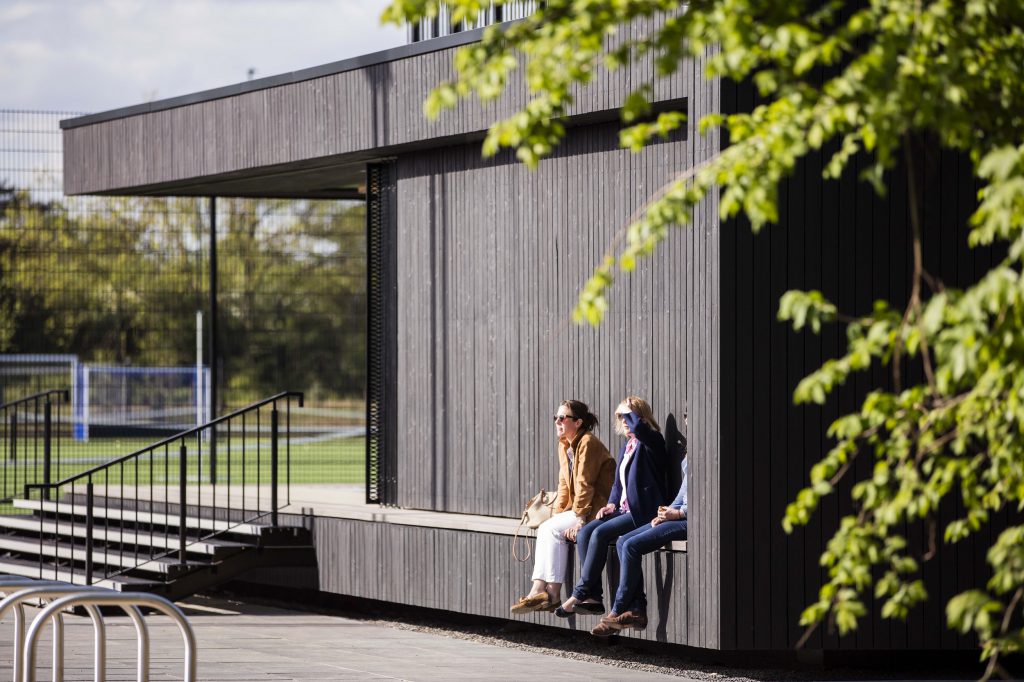
Structural Timber – the Sustainable Benefits
Environmentally, the advantages of building with structural timber are vast:
- Timber is the stand-out performer, possessing the lowest embodied carbon of any building material
- As forests are properly managed and maintained, timber provides us with the only truly renewable building resource
- Trees sequester and store carbon from the atmosphere – meaning that throughout its lifecycle, timber has a carbon negative impact.
- Timber offers exceptional energy efficiency performance, greatly reducing household emissions – a positive for both the environment and the pocket of the homeowner.
- In farmed forests, typically for every tree cut, a further five are planted.
Timber and Carbon Sequestration
Felled trees store carbon within them and timber has the lowest embodied carbon of any mainstream building material. Guided by market analysis, fire safety and structural considerations, key opportunities for the safe growth of timber use will be in low-rise buildings using traditional and certain modern methods of construction, and in a wide range of commercial and non-residential settings.
The STA will look to promote the safe use of timber in construction through several measures as stated in the Build Back Greener HM Govt. Net Zero strategy October 2021.
Atmospheric carbon is captured and stored in the biomass of the world’s forests and this process – photosynthesis – is most efficient in young-growth trees. While the global ‘carbon pool’ is declining due to deforestation, sustainable management and harvesting have seen Europe’s forests (including the UK) grow and the amount of CO2 sequestered increase by approx. 568 million tonnes per year, with the current carbon sink estimated at 135 billion tonnes of CO2. (Forest Europe Report 2020).
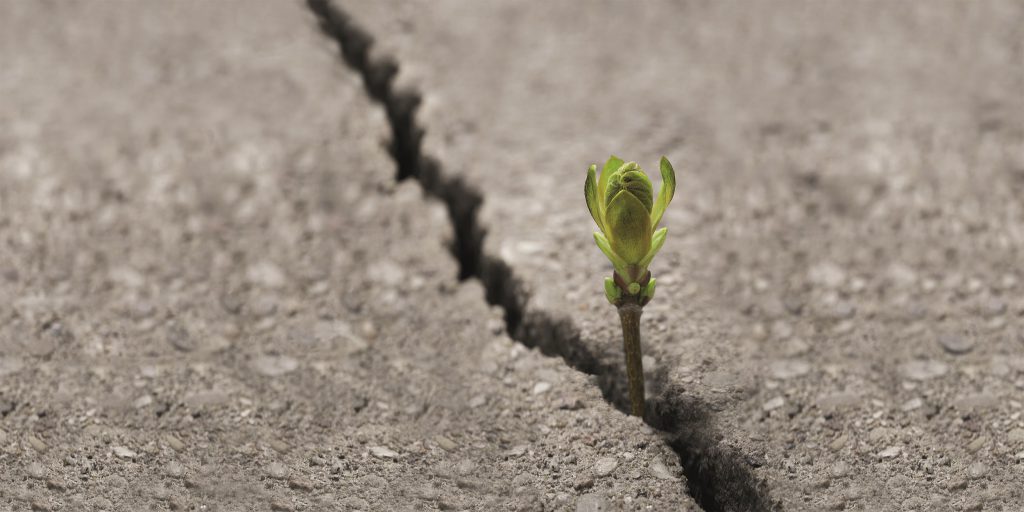

Aside from its environmentally beneficial properties, prefabricated timber frame technology could prove to be of great assistance in meeting the demand for affordable housing.
On average, using timber frame systems can reduce the construction time by eight weeks, when compared to traditional masonry methods. This is largely because timber frame is manufactured offsite and delivered as prefabricated panels that can be erected within days.
Additionally, producing timber frame systems offsite greatly improves reliability. Firstly, as they are produced in controlled factory environments, quality control is assured, resulting in fewer errors during assembly. Secondly, the fabrication of timber frame systems in a factory is not weather dependent, meaning build programmes become far more predictable. This speed of construction and greater reliability help to keep project costs low. With less labour required and fewer issues regarding quality, timber frame systems provide local authorities with the means to build more homes, at a lower cost.